Design, Installation, and Integration for Regulatory Compliance of a New Washer
Summary
Becarv delivered a comprehensive solution to upgrade a biopharmaceutical production environment involving a new washer, ensuring compliance with Eudralex Annex 1. The project included equipment installation, structural modifications, and HVAC overhaul to maintain Grade A conditions. The result: optimized environmental control, minimal downtime, and cost efficiency.
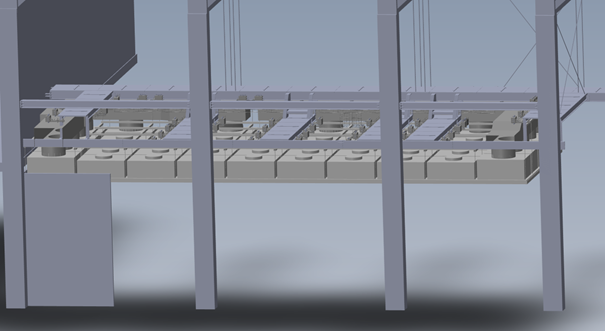
Navigating Production Constraints in a Biopharmaceutical Upgrade
In the biopharmaceutical sector, maintaining stringent environmental standards is essential for ensuring the safety and efficiency of pharmaceutical processes. Our client faced the challenge of upgrading their production environment to meet the exacting requirements of Eudralex Annex 1 Volume 4. This included the installation of a new washer and the necessary infrastructure upgrades at their site in Belgium. The objective was to maintain Grade A conditions during planned production stoppages, minimizing operational disruptions.
Becarv’s Solution
Strategic Approach to Optimizing the Production Environment
Becarv was selected to deliver a comprehensive solution, covering the design, installation, and testing of equipment to ensure full regulatory compliance. Our team conducted a thorough needs assessment to develop a solution tailored to maximize operational efficiency. The scope of the project involved:
- Structural Modifications: Demolition of existing ceilings and walls to accommodate new equipment and systems.
- New Equipment Integration: Installation of a new washer along with essential utilities such as purified water, steam, compressed air, and effluent management.
- HVAC System Overhaul: Installation of new HVAC systems, including Unidirectional Airflow (UDF) to maintain laminar unidirectional airflow crucial for cleanroom conditions.
- Seamless Integration: Ensuring the new systems worked harmoniously with existing infrastructure to minimize production disruptions.
Throughout the project, Becarv worked closely with internal teams and HVAC partners to ensure smooth integration, commissioning, and validation of all systems.
Advanced Technologies for Environmental Control and Contamination Prevention
- Autonomous Laminar Ceilings: Integrated with the new HVAC system, these ceilings helped maintain the strict airflow requirements essential for cleanroom standards.
- Customized Ventilation and Filtration Systems: Tailored to the production environment’s needs, these systems optimized air quality and minimized contamination risks.
Why They Chose Becarv’s Solution
-
Proactive Approach: Becarv’s solutions are customized to address the unique requirements and constraints of each site, ensuring optimal performance and efficiency.
-
Expertise and Quality: We provide high-quality equipment that guarantees HEPA filtration and full compliance with Good Manufacturing Practices (GMP), meeting the highest industry standards.
-
Comprehensive Support: From project initiation to completion, BECARV offers end-to-end support, with continuous monitoring and adjustments during integration to ensure seamless execution.
-
Close Collaboration: Our team works closely with internal teams and external partners, ensuring effective communication and teamwork to achieve a successful project outcome.
Quantifiable Success of BECARV’s Solution
The solutions deployed by BECARV helped our client achieve a highly controlled and compliant production environment. Key outcomes included:
- Optimized Environmental Control: The introduction of unidirectional laminar airflow reduced contamination risks and maintained cleanroom integrity.
- Minimal Operational Disruption: By efficiently managing production stoppages, the client was able to resume operations quickly with minimal downtime.
- Cost Efficiency: Seamless integration with existing systems reduced costs and complexity while ensuring regulatory compliance.