Applications
Vaccine Manufacturing Solutions
Advanced Contamination Control for Vaccine Production
Becarv provides cutting-edge cleanroom and airflow solutions tailored for vaccine manufacturing facilities. With vaccines playing a vital role in public health, our technologies ensure optimal sterility, efficiency, and regulatory compliance throughout the entire vaccine production process. Our solutions support both small-scale clinical research and large-scale commercial manufacturing to accommodate various vaccine types and production methods.
Ensuring Aseptic Conditions in Vaccine Manufacturing
Vaccine production involves multiple critical stages, including cell culture seeding, expansion, harvesting, purification, and final formulation. Maintaining aseptic conditions is essential at every phase, which is why Becarv’s Laminar Airflow (LAF) systems and Fan Filter Units (FFU) play a crucial role in:
- Providing unidirectional airflow to prevent airborne contamination
- Filtering particles and microorganisms with HEPA and ULPA filtration
- Ensuring consistent cleanroom conditions to meet stringent regulatory standards
To further enhance process sterility, Becarv’s Closed Seeding Unit offers an automated closed-system approach for cell culture seeding, reducing contamination risks and ensuring greater control from the earliest stage of vaccine production.
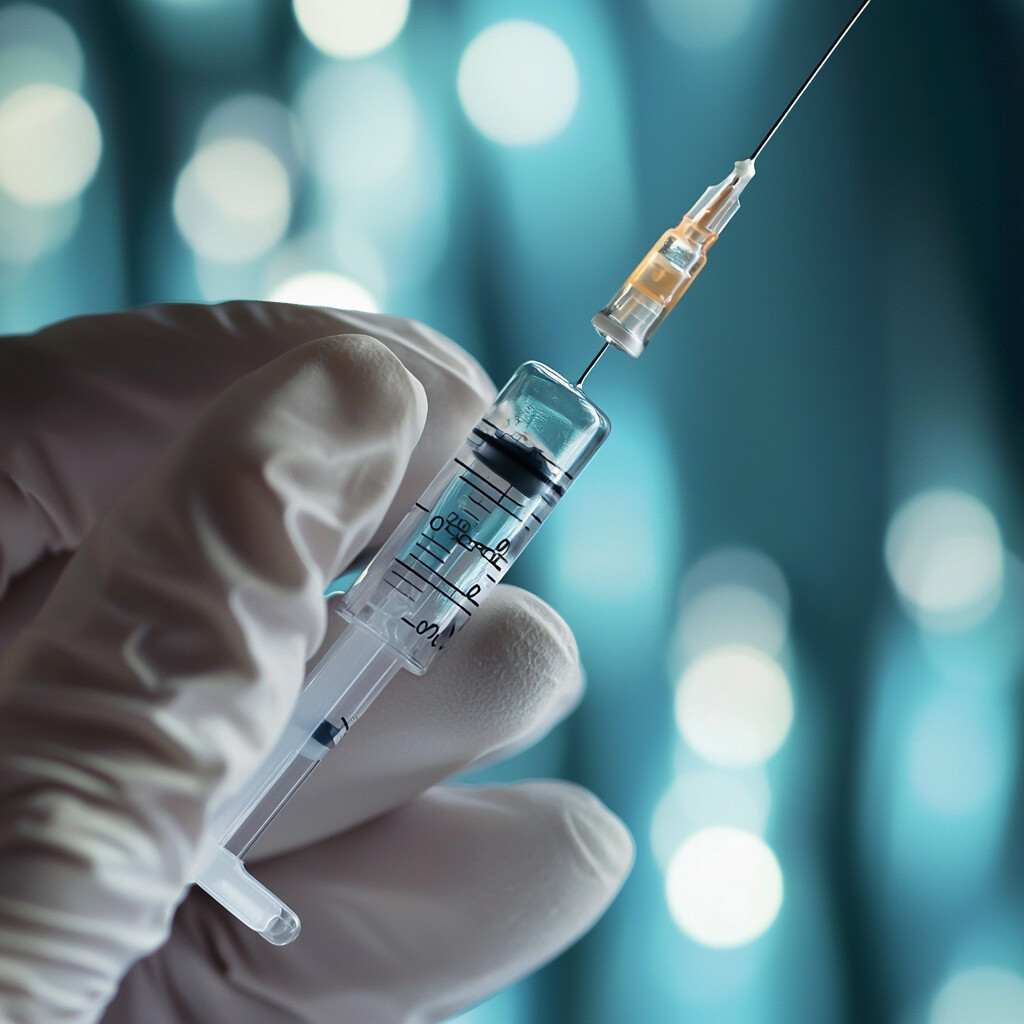
Flexible & Scalable Solutions for Various Vaccine Types
Vaccine manufacturing processes differ based on production methods, including:
- Egg-based production – Common for flu vaccines, requiring strict contamination control
- Cell culture-based methods – Used for viral vector and recombinant protein vaccines
- Recombinant protein expression systems – Applied in bacterial, yeast, and mammalian cell-based vaccine development
Becarv’s customizable cleanroom solutions support all these production methods, ensuring sterile and adaptable environments to accommodate different vaccine formulations and production scales.
Regulatory Compliance and Controlled Environments
Becarv’s solutions comply with EudraLex Annex 1 Volume 4 guidelines, ensuring:
- Proper airflow management in critical processing zones
- Optimal contamination control during aseptic production
- Integration of high-efficiency filtration systems to meet industry regulations
By strategically positioning FFU and LAF systems, vaccine manufacturers can maintain process sterility, minimize contamination risks, and ensure regulatory compliance in critical production zones such as:
- Washing and wrapping workstations
- Sterilization and post-sterilization areas
- Packaging stations before sterilization or irradiation
Why Choose Becarv for Vaccine Manufacturing?
- Trusted by leading vaccine manufacturers with solutions adaptable to both small and large-scale production
- Modular and scalable cleanroom technologies for seamless facility expansion
- Advanced contamination control with HEPA/ULPA filtration to maintain sterility
- Full regulatory compliance with industry standards and cGMP guidelines
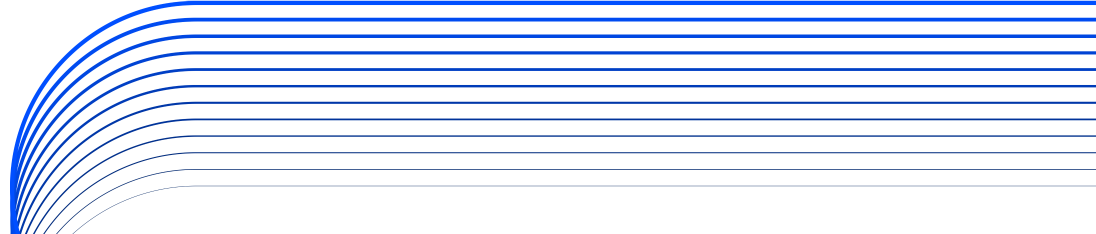
Monoclonal Antibody Production Solutions
Precision-Engineered Contamination Control for mAb Manufacturing
Monoclonal antibody (mAb) production demands strict environmental control to maintain high product quality, sterility, and regulatory compliance. Becarv’s specialized cleanroom solutions, including Closed Seeding Units and Modular Airflow Systems, are designed to support every stage of the mAb manufacturing process, ensuring optimal conditions from cell culture to final formulation.
Critical Systems for Monoclonal Antibody Manufacturing
- Closed Seeding Unit – Automates cell culture seeding, reducing manual handling and contamination risks
- Modular Airflow Systems (FFU & LAF) – Maintain aseptic conditions in bioreactor rooms, chromatography labs, and fill/finish areas
- HEPA and ULPA Filtration – Ensure effective airborne contaminant removal for sterility compliance
Becarv’s solutions help increase production efficiency, minimize risks, and support regulatory adherence in all key stages of mAb development and production.
Key Applications in Monoclonal Antibody Manufacturing
- Cell Culture & Bioreactor Environments – The Closed Seeding Unit automates cell culture seeding, reducing operator exposure
- Aseptic Processing & Fill/Finish Areas – Laminar airflow ensures sterile conditions during final formulation and packaging
- Purification & Chromatography – Supports controlled environments for precise mAb purification
Why Choose Becarv for Monoclonal Antibody Production?
- Optimized process efficiency with automated cell seeding and contamination control
- Compliant with cGMP, FDA, and global biopharma manufacturing standards
- Modular and scalable systems adaptable for both research and large-scale production
Cell and Gene Therapeutic Solutions
Automated Contamination Control for Advanced Therapies
Cell and gene therapy manufacturing involves highly specialized processes, requiring strict sterility control to ensure patient safety and regulatory compliance. Becarv’s Closed Seeding Unit automates critical steps in cell culture seeding and expansion, reducing human intervention and improving process consistency.
Enhancing Contamination Control with Automation
Unlike traditional manual processes, which introduce contamination risks, Becarv’s Closed Seeding Unit offers:
- A fully automated, closed-system approach to minimize contamination
- A single-use kit system for improved sterility and traceability
- Digitalized real-time monitoring to ensure compliance with regulatory standards
Key Applications in Cell & Gene Therapy Manufacturing
- Cell Therapy Manufacturing – Automates cell culture seeding for autologous and allogeneic therapies
- Viral Vector Production – Maintains contamination-free conditions for gene therapy applications
- Cell Banking – Ensures sterility in Master Cell Bank (MCB) and Working Cell Bank (WCB) expansion
Why Choose Becarv for Cell & Gene Therapy?
- Advanced sterility solutions that support automated, contamination-free processing
- Regulatory-compliant systems for cGMP and FDA-regulated cell therapy manufacturing
- Scalable cleanroom technologies designed for clinical and commercial applications
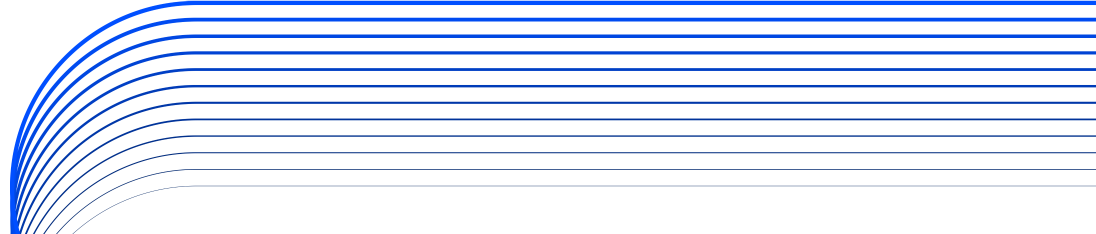